Robotic Finish Grinding System
The company’s specialized casting process is typically leveraged towards low volume runs, with a high mix of different parts. Therefore, the system would need to be designed to meet the following objectives:
- Ability to accommodate frequent part changeovers, with minimal downtime
- Ease of programming (new part path generation)
- Achieve a consistent, uniform finish
- Achieve a repeatable cycle time and higher throughput
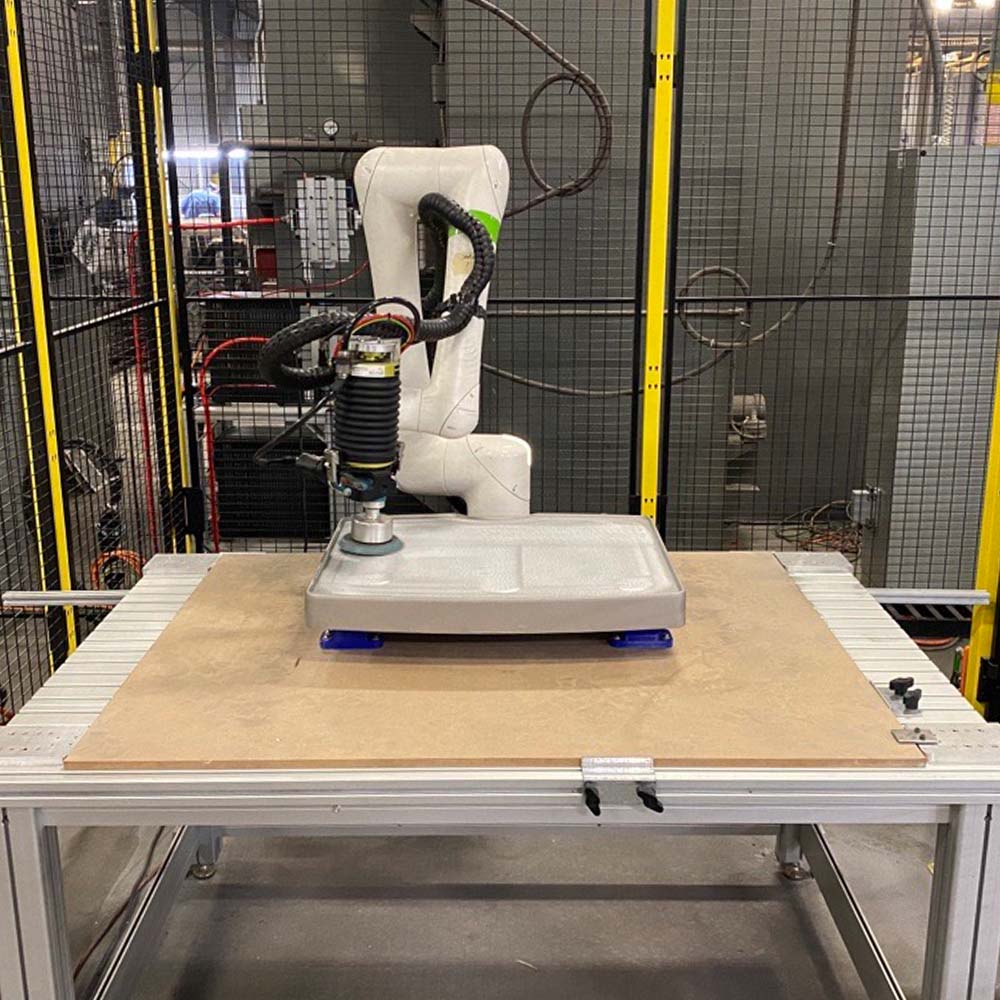
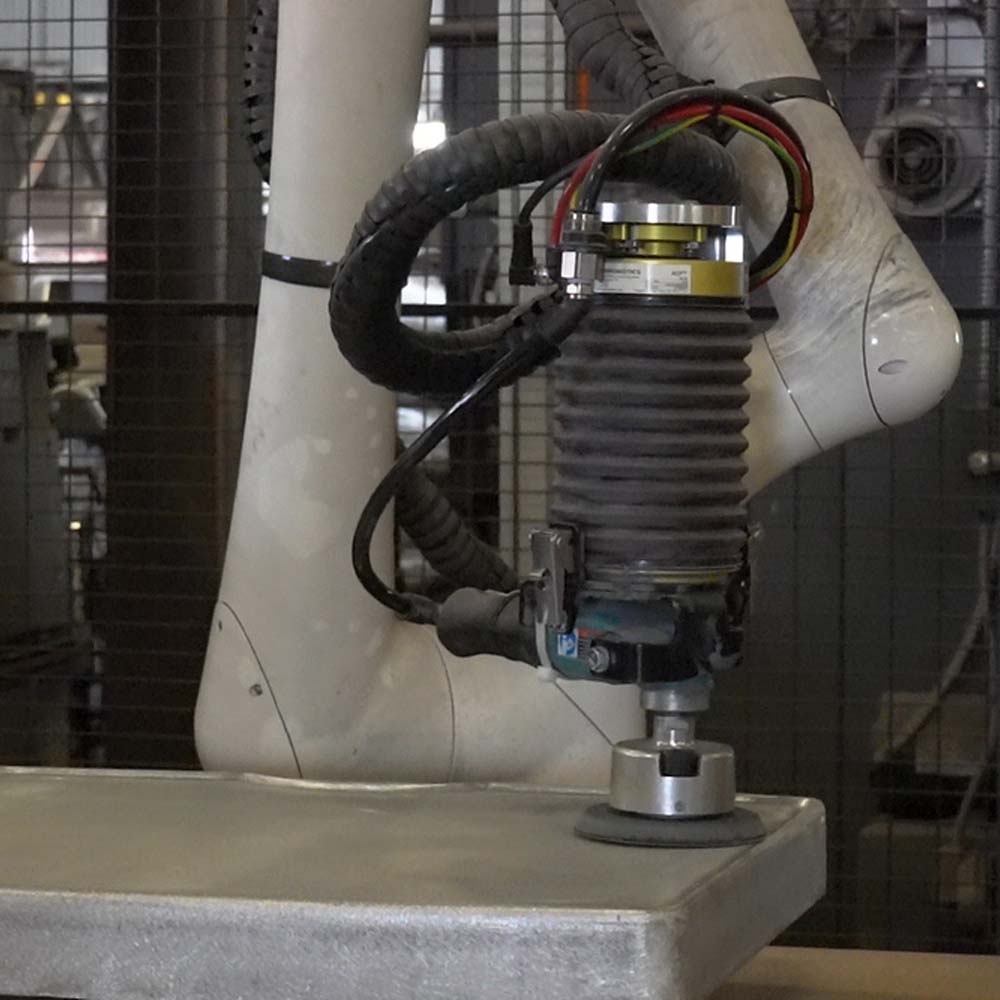
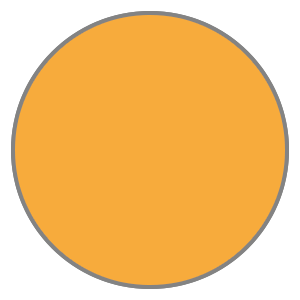
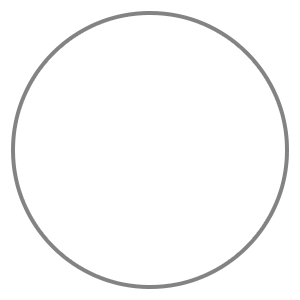
- A Fanuc CRX collaborative robot mounted onto a Macron Dynamic’s RTU (robot transport unit).
- Each robot was equipped with a Dynabrade 5” orbital sander attached to a Ferrobotics ACF (active contact flange).
- Two part load/unload stations, each comprised of a t-slot table and a safety mat
- Dedicated part fixtures, constructed from low-cost MDF “bread” boards and applied 3D printed fixture blocks, would be loaded/unloaded onto the tables by an operator.
- The safety mat would detect the presence of an operator (at a station) and the robot would be inhibited from this station by Fanuc’s dual check safety (DCS) software.
- Robot motion path programs were generated for each part face using a combination of hand teaching and Fanuc’s Roboguide simulation software.
- Process adjustments for grind force, robot speed, and motion path can be made through a local HMI.
- Additional features of the system included using the robot to touch off on a part for part verification, logging of the time on part for predictive media change, and an overhead monitor to display OEE production data.
Benefits:
- The system arrangement minimizes downtime, by providing the ability for an operator to exchange a part at one part station, while the robot processes a part at the other part station.
- The dedicated MDF boards eliminate the time required to tear down and erect traditional modular workholding fixtures.
- The ACF is a compliance device which delivers a constant, programmable force of the media against the part, ensuring a consistent uniform finish.
- The CRX robot includes a hand-teaching function, facilitating motion path teaching and touch-up.
Result: Premier delivers a custom automated solution that meets the customer’s objectives of a reduction in labor strain, repeatable & improved part quality, and higher throughput.