Robotic Palletizing of Custom Products
Design constraints:
- Accurately locate parts on an infeed table for the robot to pick
- Integrate the robot and inspection equipment with the rest of the production line
- Allow flexibility for multiple part width’s and stacking patterns based on part geometry
- Very tight space constraints at the end of the line for the robotic cell
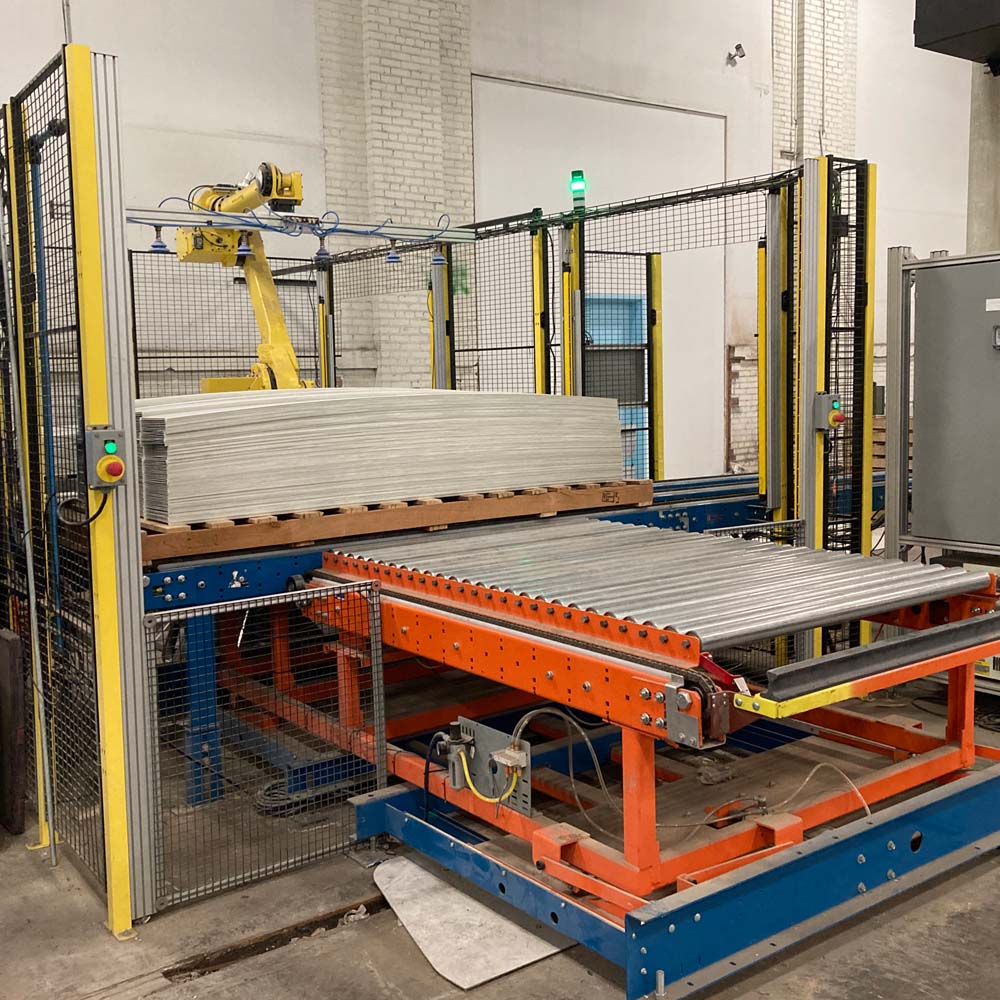
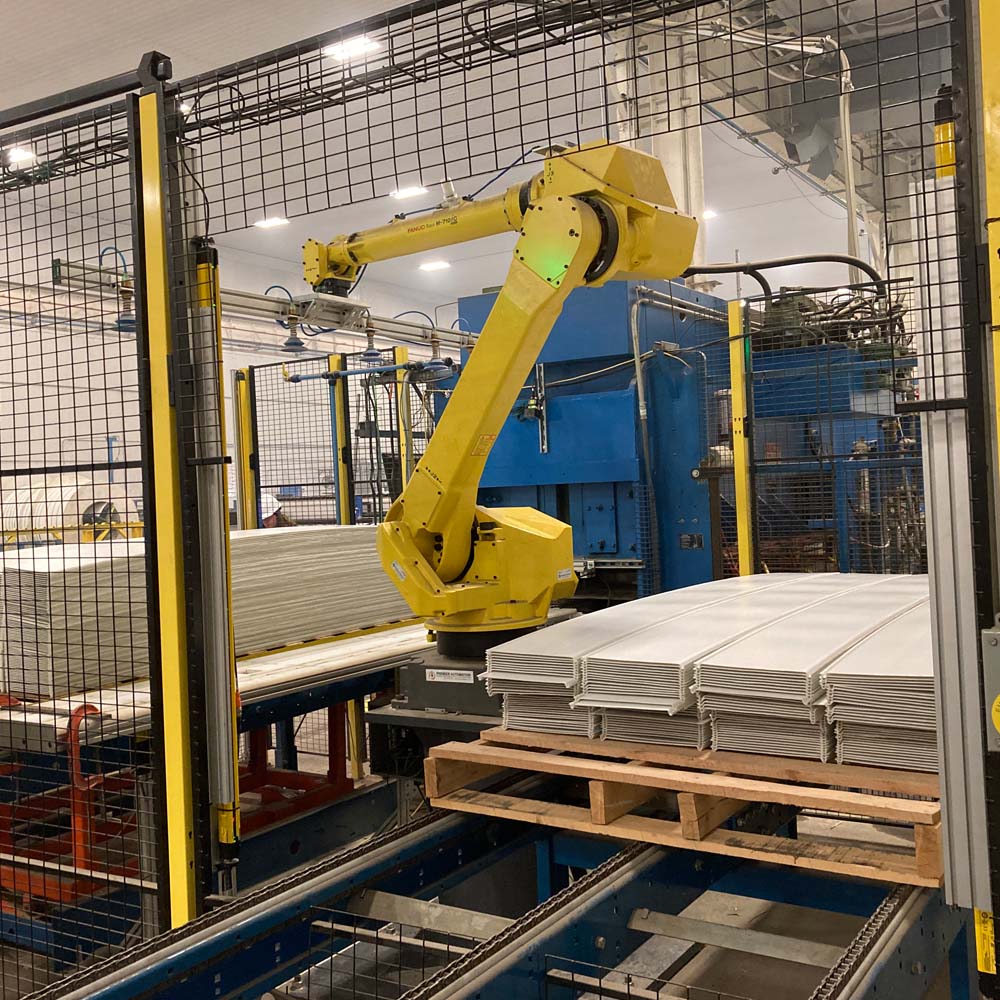
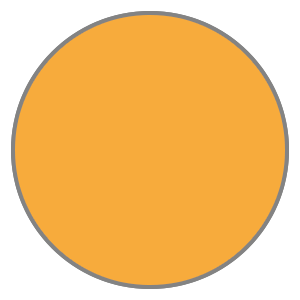
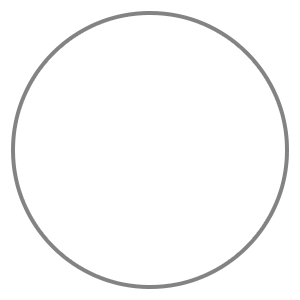
Challenges during the development and integration of this system included keeping the stacks straight and stable as they got near the max height of the pallet. Completed pallets would have parts stacked up to 42” high. Due to the part geometry, the stacks tended to lean one direction and make aligning the geometry of each part much more difficult.
Results & Impact to Customer: Premier automation delivered a custom palletizing solution that meets the customer’s objectives of consistent palletizing, reduced operator interaction, and improved in-line process inspection.