Heavy Payload Machine Tending Robot
Train wheels come to the customer as a raw forging with very rough dimensions. The machining process can remove upwards of 500lbs of material from a single wheel. The robot and tooling had to be sized to accommodate parts up to 1200lbs, and flexible enough to handle both the raw forging and finish machined parts without requiring a tool change.
Design Constraints:
- Accurately locate parts of varying diameters and heights on an infeed table for the robot to pick
- Provide adequate clearance between the CNC door opening and the robotic gripper
- Robot tooling must be able to handle a diameter range from 24-48"
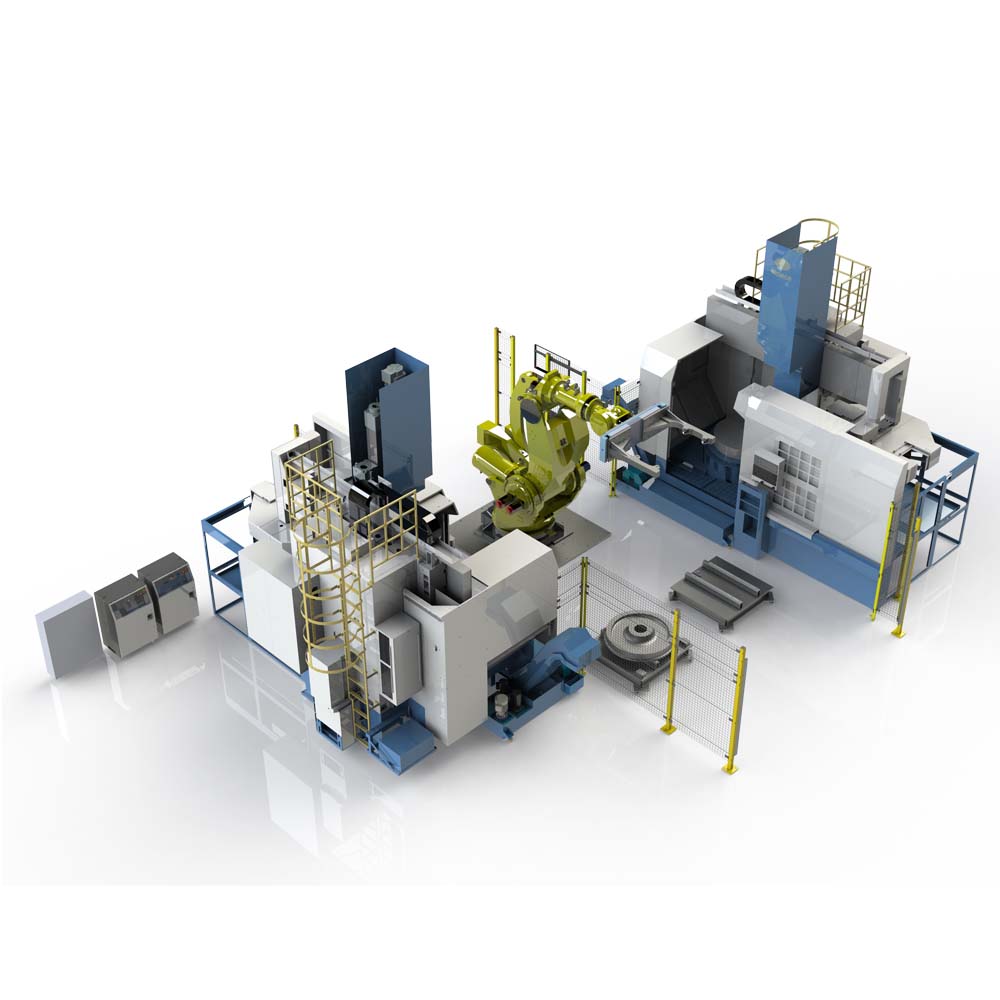
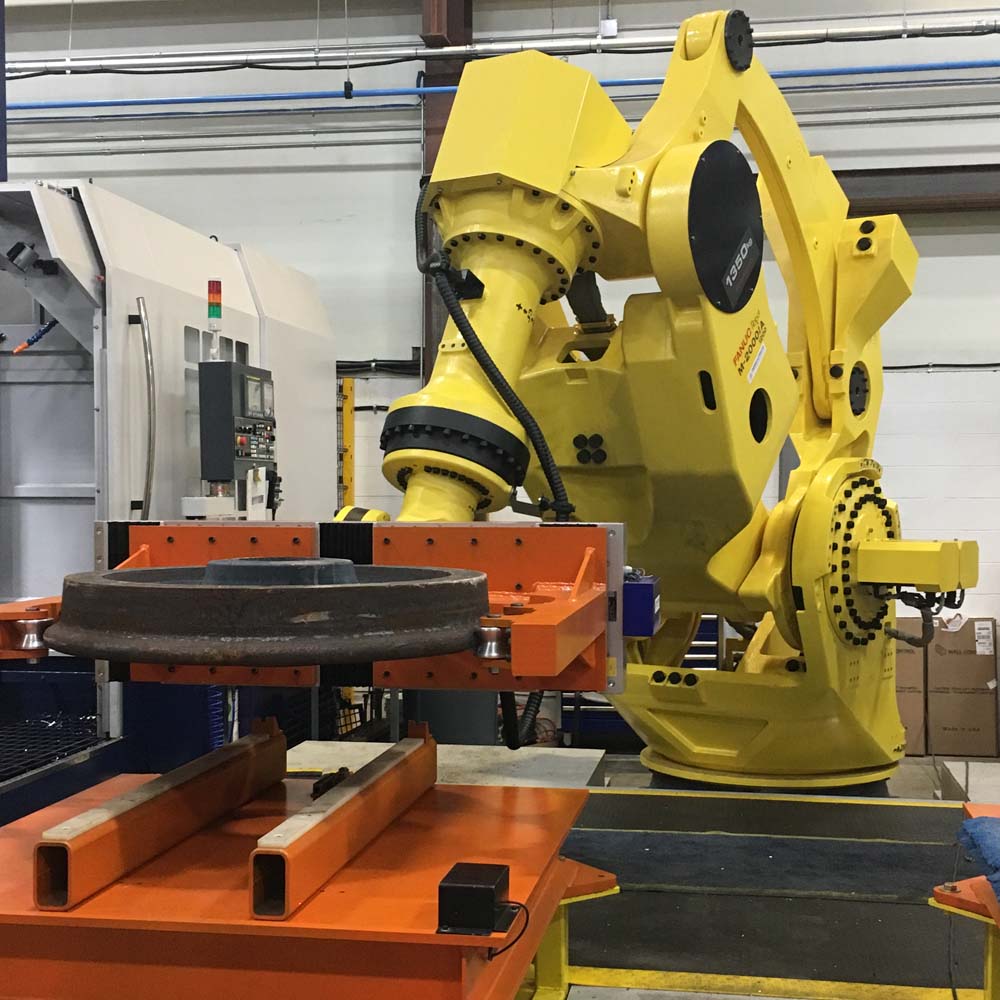
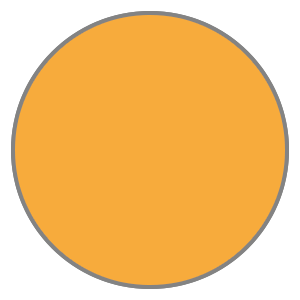
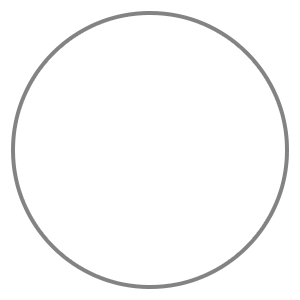
Results and Impact to Customer: Premier Automation delivered a custom automated solution that meets the customer’s objectives of improved safety for operators when handling parts and improving the flexibility of the system to handle a wide range of wheel geometry.