Large Part Material Handling Robots in Mill Environment
Objectives:
- Replace two robots nearing their end of life with new Fanuc robots
- Replace a custom inverted linear rail with a new custom Rollon-IMS RTUi. This rail acted as a 7th axis for an underslung robot in the mill pit
- Modify and improve tooling to adapt to new robots
- Incorporate operator feedback into the mechanical design and teaching process for the system
Design Constraints:
- Spec two new robots and a linear rail unit that will match payload, reach, and fit within the footprint of the existing system
- The existing system had incredibly tight space constraints with the customers facility, with one robot operating in a pit and very close to structural beams within the facility
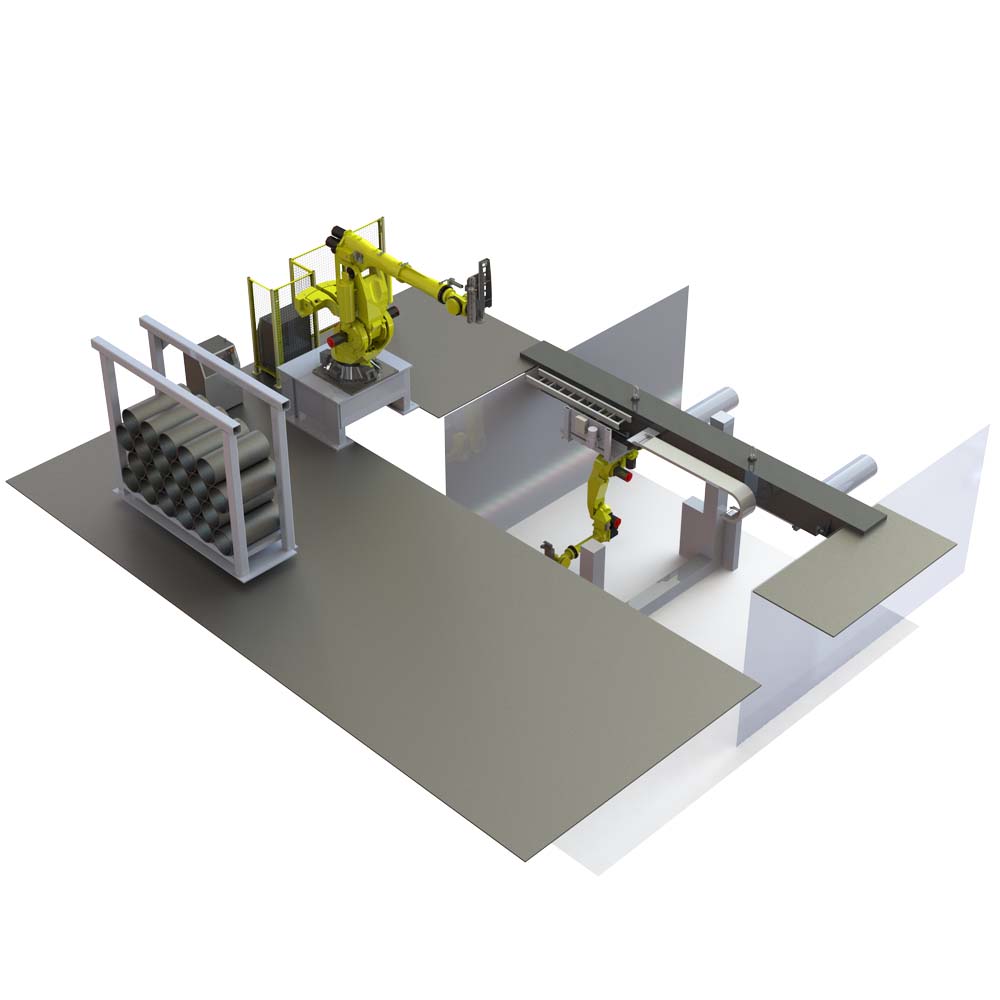
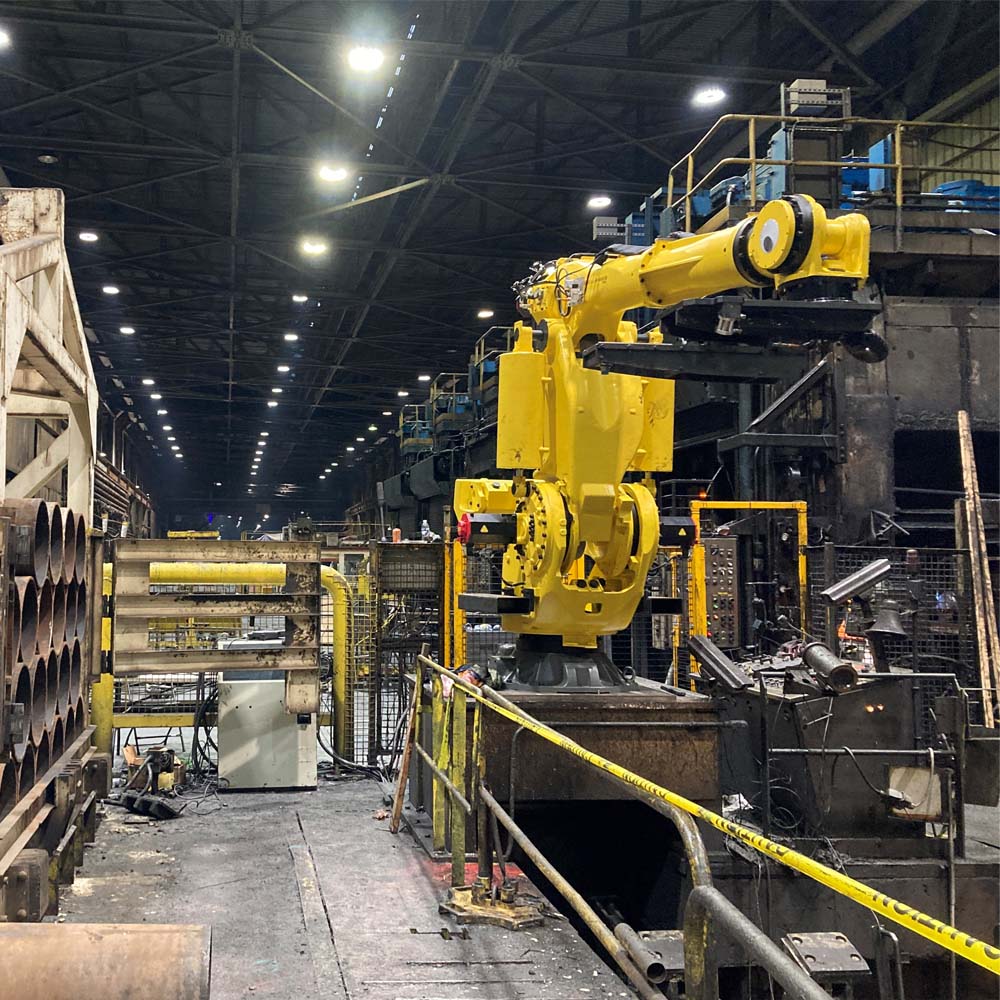
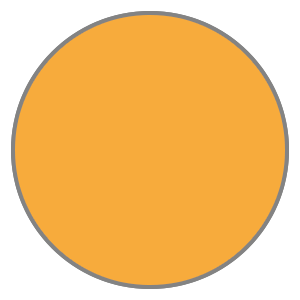
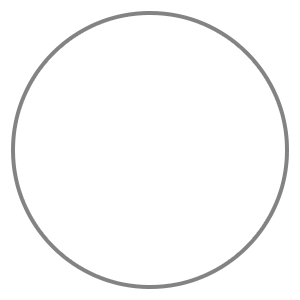
Results and Impact to Customer: Premier successfully took on this challenge to replace both robots and an inverted linear rail with new equipment for the customer. Each objective for the project was successfully met, and now the customer is currently back to running the mill with the robots at full capacity.