Robotic Rack Unloading Cell for Automotive Windows
The material handling cell would be located at the beginning of a vinyl trim and washer line. The cell needed to handle a variety of glass shapes and sizes, ranging from 20” x 20” to 40” x 40”. The autoclave racks were comprised of three slotted Teflon rails, which were used to contain and separate the windows from one another. The cell had to meet the following requirements:
- Ability to accommodate frequent part changeovers, with minimal downtime.
- No glass-to-glass contact within the racks.
- Achieve a 12 second cycle time.
- To achieve the desired rate of output the line could not be shut down for the exchange of an empty rack with a full rack. Therefore, a method of unloading one rack while another rack was exchanged was necessary.
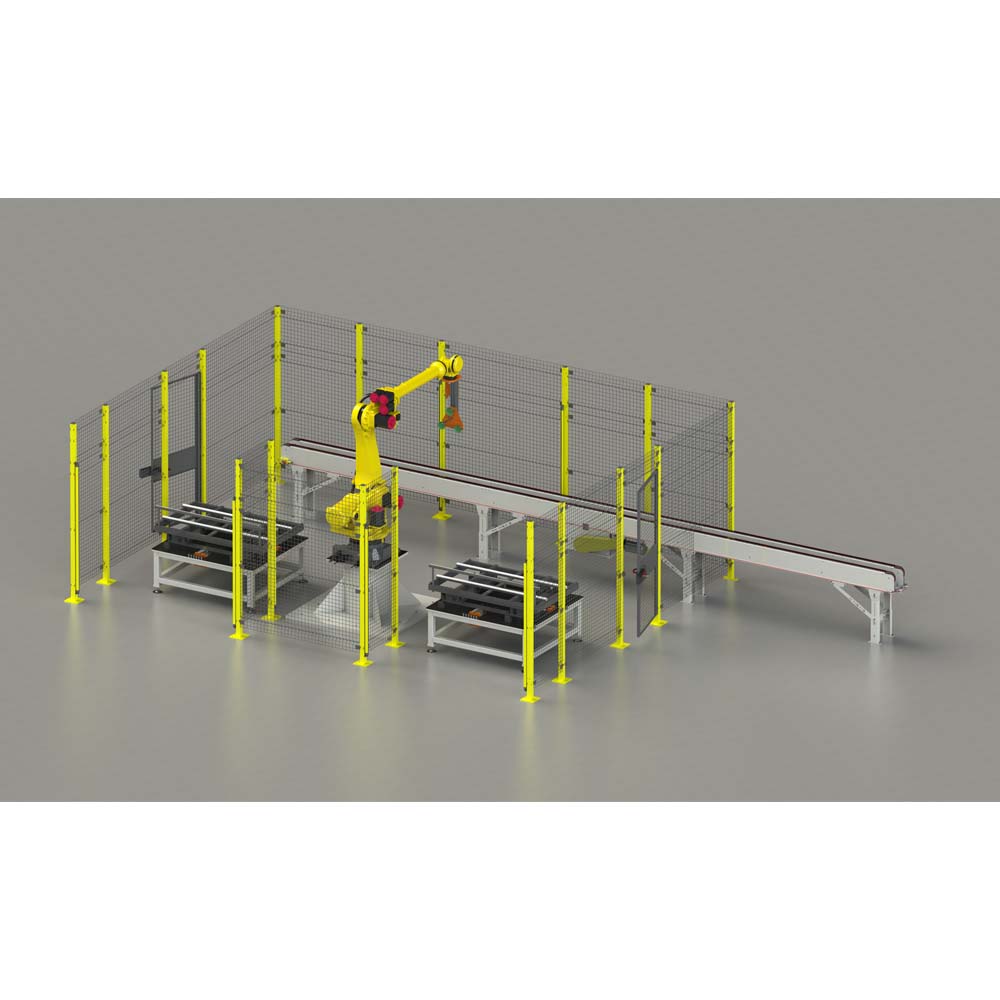
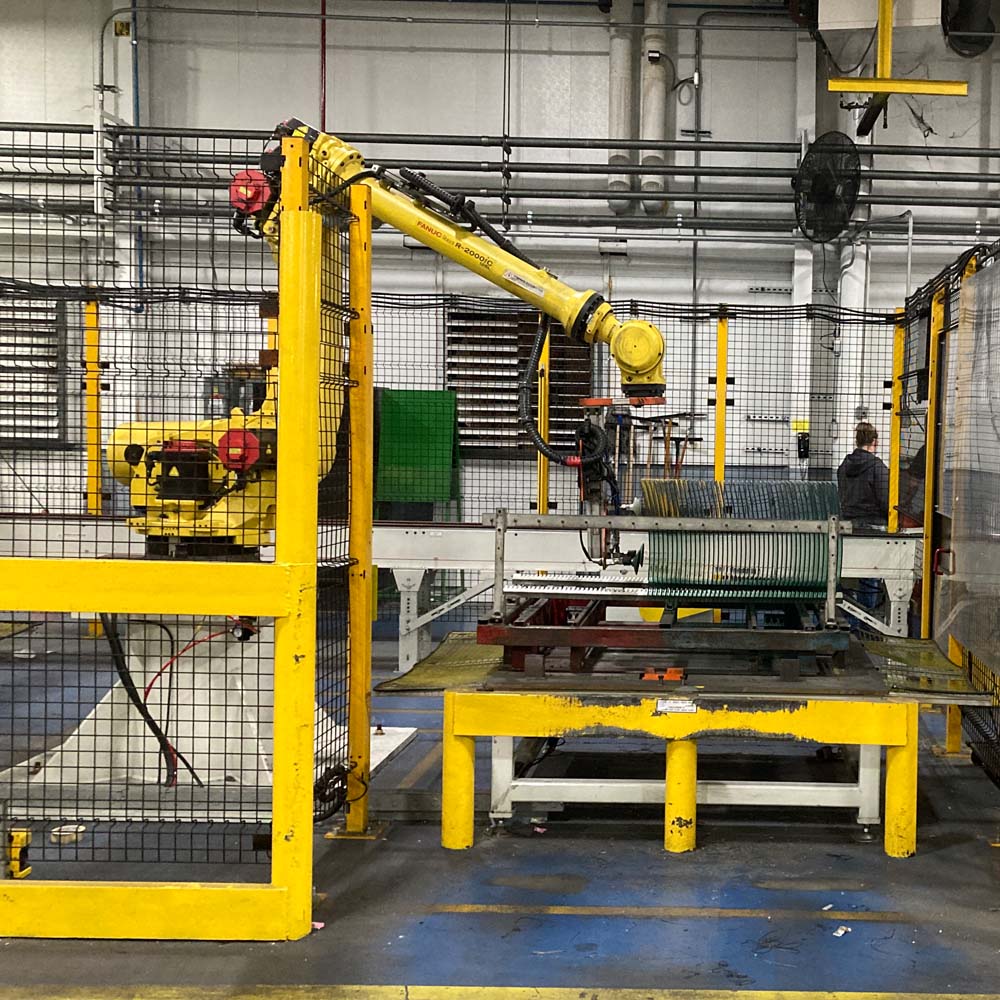
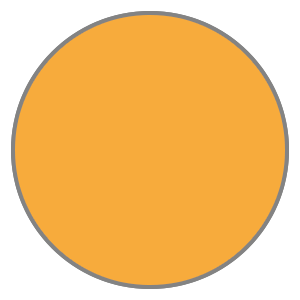
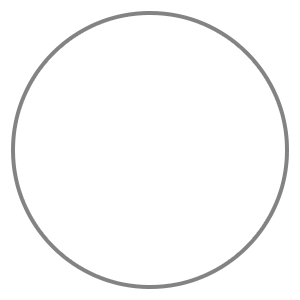
- A Fanuc R-2000/125L, 6-axis industrial robot collaborative robot equipped with a vacuum gripper.
- Two rack load/unload stations, each comprised of a fabricated rack stand which would register and clamp the rack into a corner.
- Each rack station would include an outside and inside light curtain set. The outside light curtain set would be active during the unloading of a rack by the robot. The inside light curtain set would be active during an empty-to-full rack exchange. The robot would be inhibited from the exchange location by Fanuc’s dual check safety (DCS) software.
- An ultrasonic sensor (onboard the robot) would be used to discover the absence/presence, and vertical “lean”, of the windows within the racks.
Benefits:
- The two rack load/unload stations eliminated downtime, by providing the ability for a rack exchange at one rack station, while the robot unloaded a rack at the other rack load/unload station.
- The strategy of using the ultrasonic sensor, to discover the vertical “lean” of the windows, enabled the robot to pick the glass with its vacuum gripper without pushing the window against the one behind it.
Result: Premier delivers a custom automated material handling solution that meets the customer’s objectives for redeployment of labor, zero downtime, and the accurate handling of product.