Robotic Rack Loading Cell for Automotive Windows
The material handling cell would be located at the end of a window lamination line. The cell needed to handle a variety of glass shapes and sizes, ranging from 20” x 20” to 40” x 40”. The autoclave racks were comprised of three slotted Teflon rails, which were used to contain and separate the windows from one another. The cell had to meet the following requirements:
- Ability to accommodate frequent part changeovers, with minimal downtime.
- Ability to confirm the setup of the Teflon rails (on the racks), as their locations varied according to the size and shape of window that was running on the line.
- Ability to locate the slots in the Teflon rails as they may not be consistent in size and location due to wear and creep/growth from repeated heating and cooling cycles.
- No glass-to-glass contact within the racks.
- Achieve a 12 second cycle time.
- The assembly line could not be shut down while windows were running at steady state. Therefore, a method of loading into two autoclave racks, one being loaded and one ready for loading, was necessary.
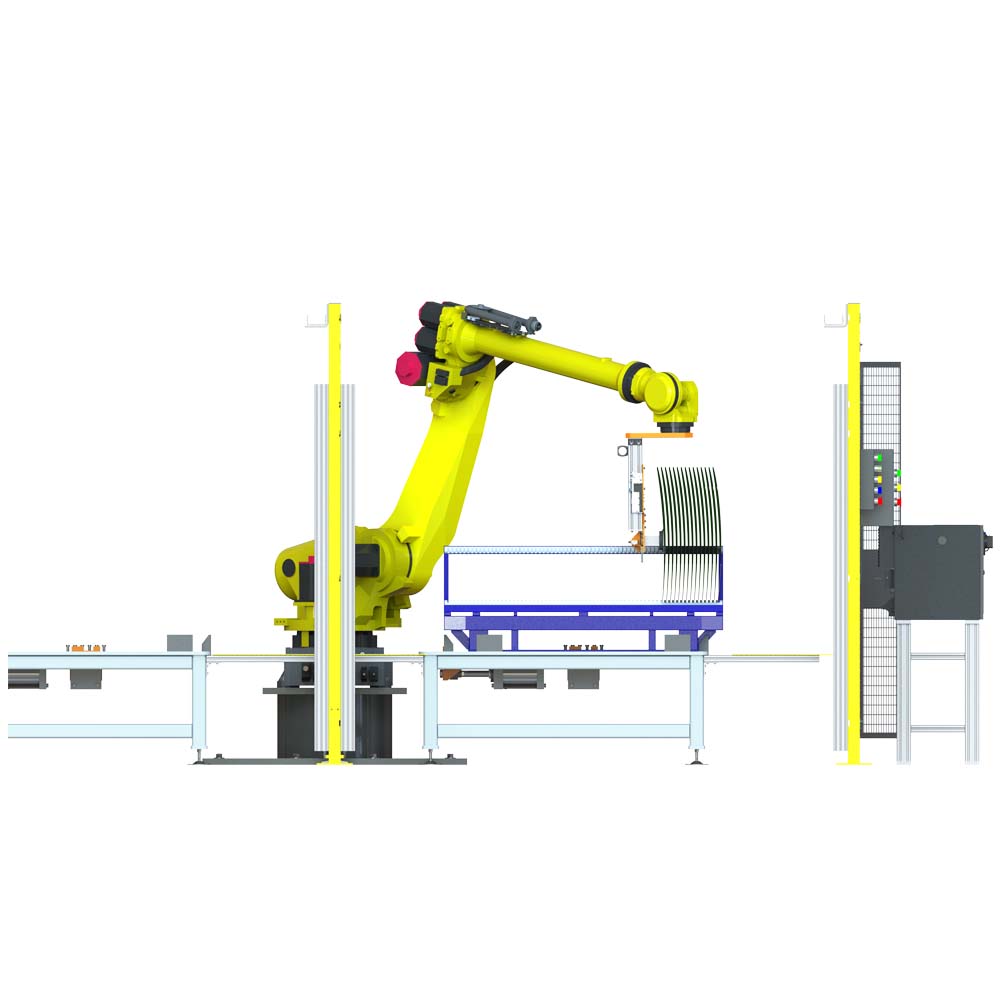
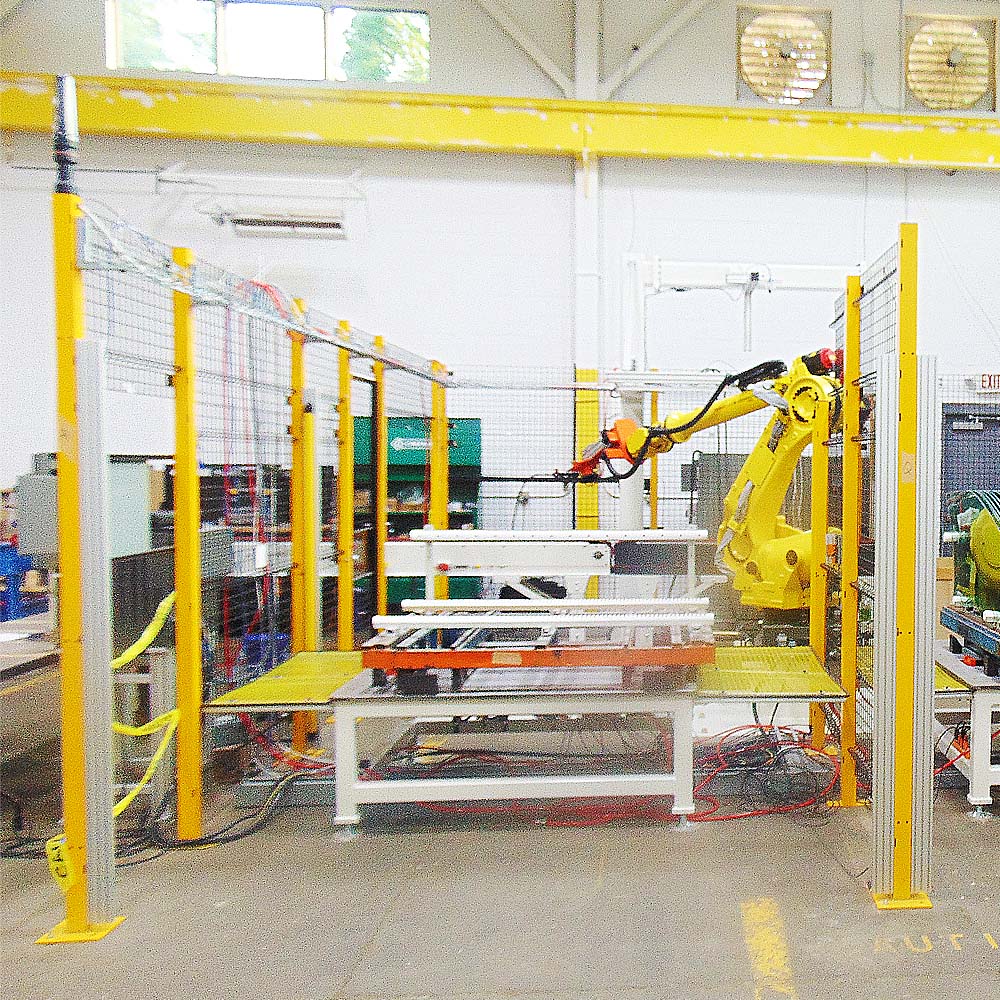
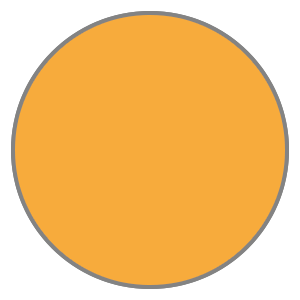
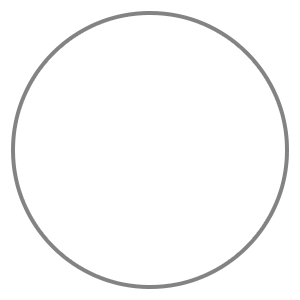
- A Fanuc R-2000/125L, 6-axis industrial robot collaborative robot equipped with a vacuum gripper.
- Two rack load/unload stations, each comprised of a fabricated rack stand which would register and clamp the rack into a corner.
- Each rack station would include an outside and inside light curtain set. The outside light curtain set would be active during the loading of a rack by the robot. The inside light curtain set would be active during a full-to-empty rack exchange. The robot would be inhibited from exchange location by Fanuc’s dual check safety (DCS) software.
- An optical fork sensor (onboard the robot) would be used to find (scan) the location of the slots in the Teflon rails. The robot would move the sensor across each rail at a known speed. A high/low input from the sensor would be used to “map” the locations of the slots, relevant to the robot’s coordinate system. A proprietary algorithm would convert the data into a position that the robot would use to engage the window with the slots.
- Additional features of the system included a vision system used for the acquisition of glass on the cell’s infeed conveyor.
Benefits:
- The two rack load/unload stations eliminated downtime, by providing the ability for a rack exchange at one rack station, while the robot loaded a rack at the other rack load/unload station.
- The strategy of using the optical fork sensor, to scan the slots in the Teflon rails eliminated the need for tooling changeovers or adjustments; and the need for a higher-priced, more complicated vision system to image the notches in the rails.
Result: Premier delivers a custom automated material handling solution that meets the customer’s objectives for rate, redeployment of labor, zero downtime, and accurate placement/handling of product.