Robotic Dispensing, Screw Driving, and Pallet Conveying System
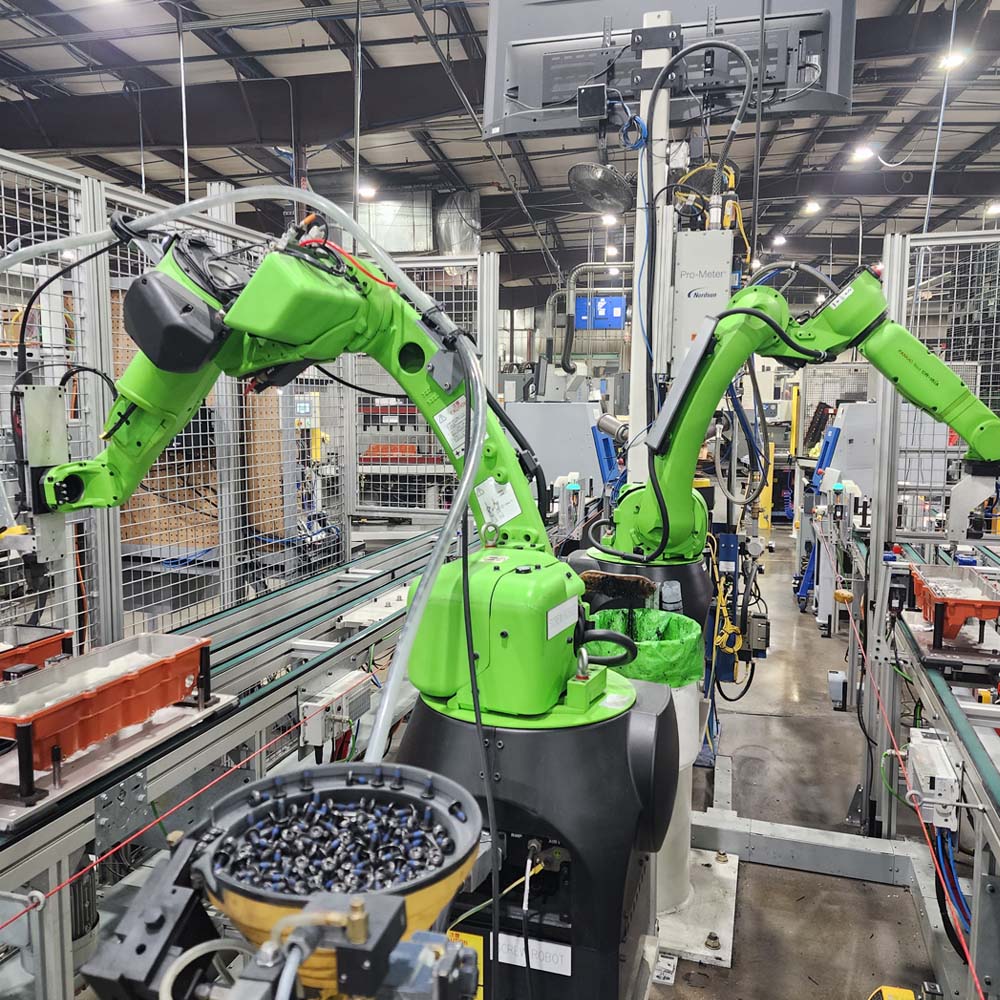
The objective for Premier was to design a semi-automated system for the manufacturing of valve cover assemblies, with robots handling the processes that require the most accuracy and consistency such as dispensing and screw driving. Operators would handle the less automation-friendly processes to save on cost. Each valve cover had to be accurately tracked throughout each stage of the system, with inspection data for each process recorded and saved to an external server.
The Challenges:
- Use a robot with an automated dispensing system to create a uniform bead of material along the complex geometry of each valve covers
- Accurately track parts throughout each step of the system and record critical process parameters to a database
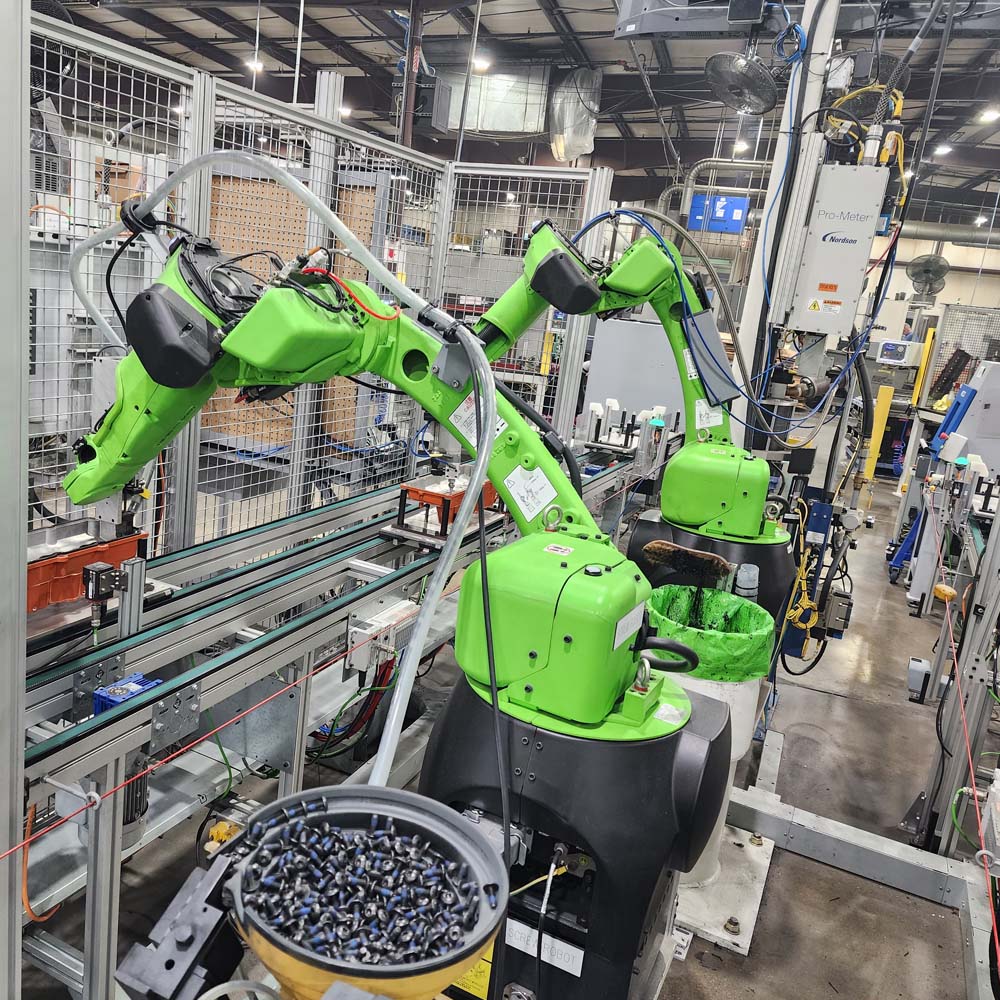
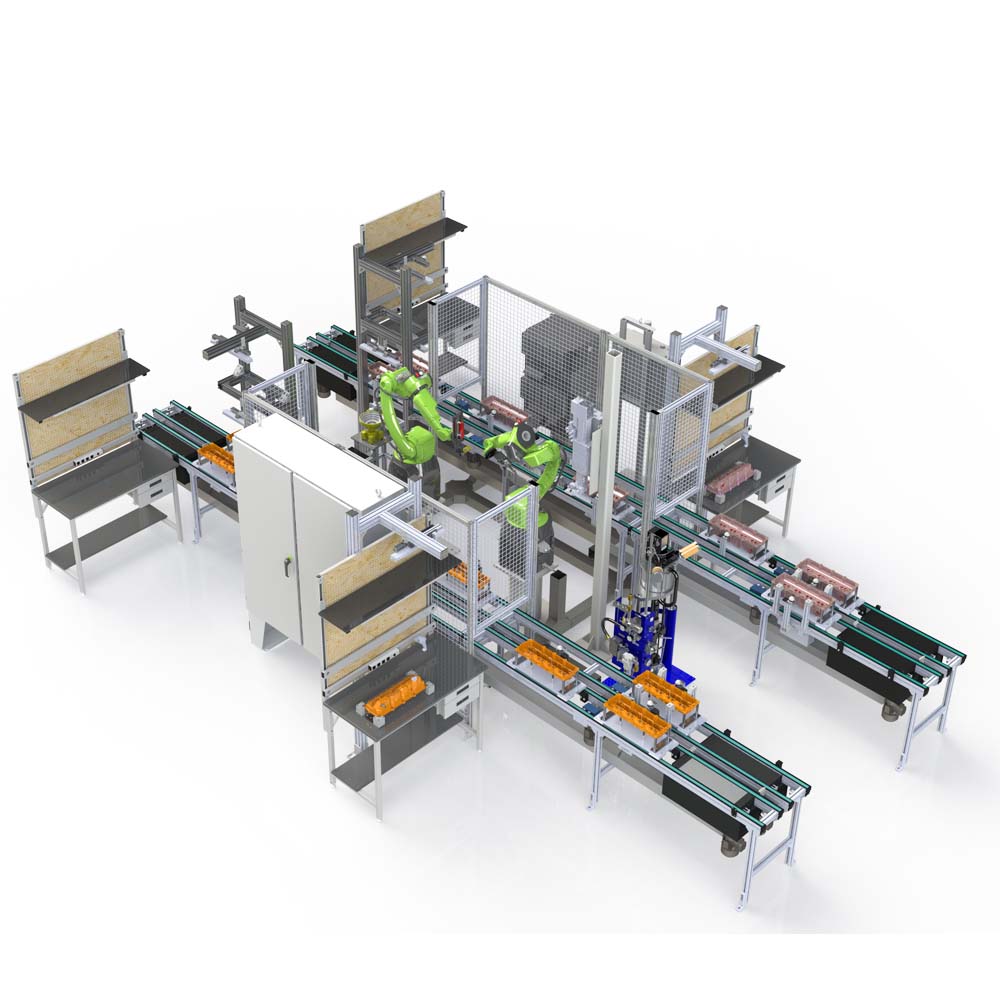
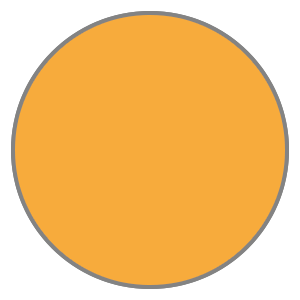
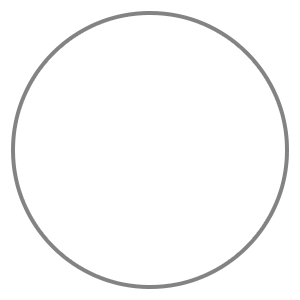
An operator would load a valve cover on the first station of the line using custom fixturing to guide the part onto a dedicated pallet fixture. The pallet and part would then index to the first robot station for automated bead dispensing. This robot was equipped with a Nordson Auto-Flow dispense valve, and a Rhino SD2 pump and bulk unloader specialized for use with RTV silicone material. The dispensing robot would traverse over 800 different points along the bead profile to complete this step of the process. Fanuc cad to path software was used to efficiently generate the dispensing programs. Upon completion, the part indexes to a Keyence 2D vision system to inspect the bead profile on each valve cover for quality control.
After successful inspection, an operator places a separator plate atop the RTV bead that was dispensed, along with a series of gaskets at other locations on the part. The valve cover is then inspected again by the vision equipment to ensure quality control of the manual gasket insertion.
On to the next step of the assembly process, the part indexes to the second robot equipped with a Design Tool Inc. Autofeed screw driving system. This system would automatically feed screws from a vibratory bowl feeder in bulk to an automated screwdriver. This station inserts up to 7 screws to secure the separator plate to the valve cover casting, while also ensuring each screw is torqued to the proper specifications.
Finally, the valve cover indexes to another operator station to be removed from the pallet fixture, flipped, and placed onto an external workbench fixture to apply additional components to the opposite face of the part.
Throughout the process, each station had a Keyence barcode reader to track parts accurately through each station of the system. Data from each inspection process was uploaded to a server and linked to each part’s unique barcode to ensure the highest quality parts are being assembled.
Impact to Customer & Results: The major benefits realized by the customer were the following:
- Simplified process flow from start to finished assembly
- Improved quality control and data collection of all critical processes throughout the assembly
- Ease of expanding the system to incorporate new parts with dedicated pallet fixtures and barcodes readers at each station