Custom Assembly System for Automotive Gear Components
The gears have three rectangular slots on each face. Each slot would receive a cylindrical magnet. The magnets were to be bonded into the slots using a cyanoacrylate glue. The magnets are introduced into the system unmagnetized and are magnetized after they are installed into the gears. The system would need to be designed to meet the following objectives:
- The magnets and gears needed to be bulk fed into the system.
- The system had to achieve a rate of output of 240 gears per hour.
- The system had to be designed to operate 24/7.
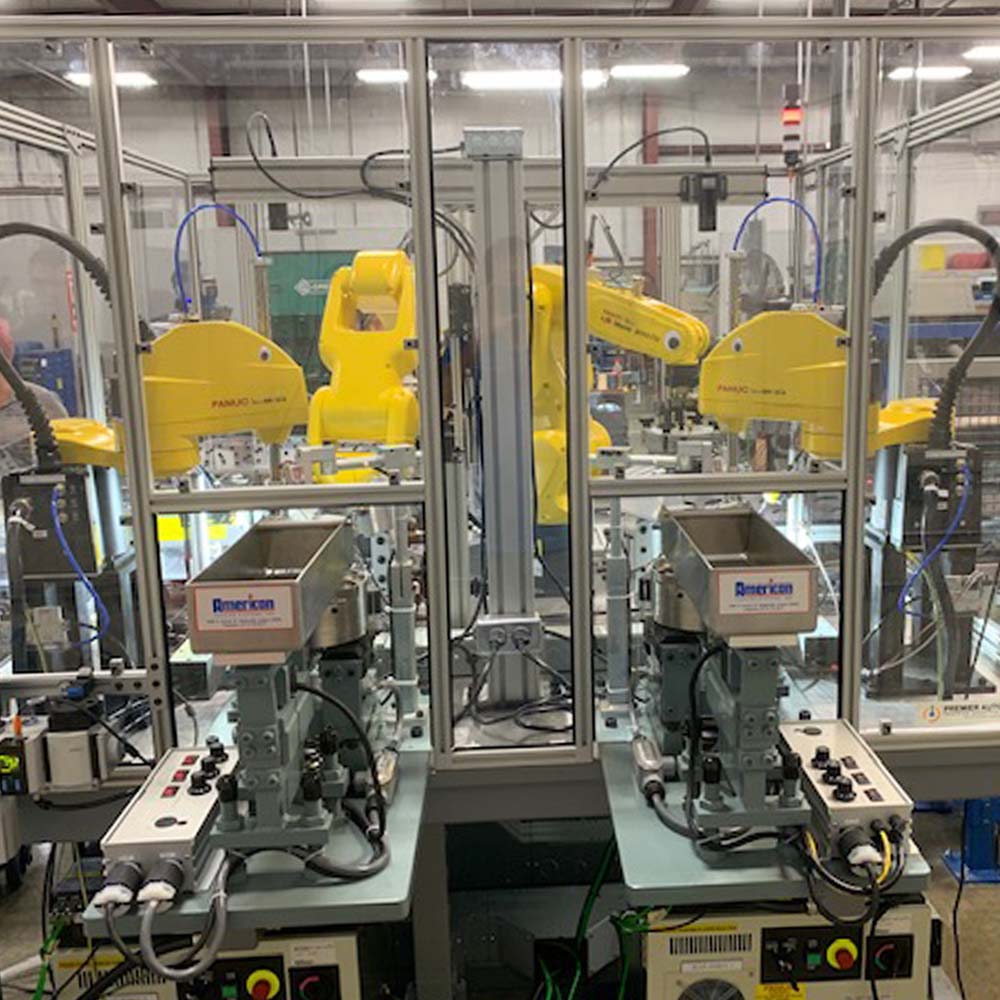
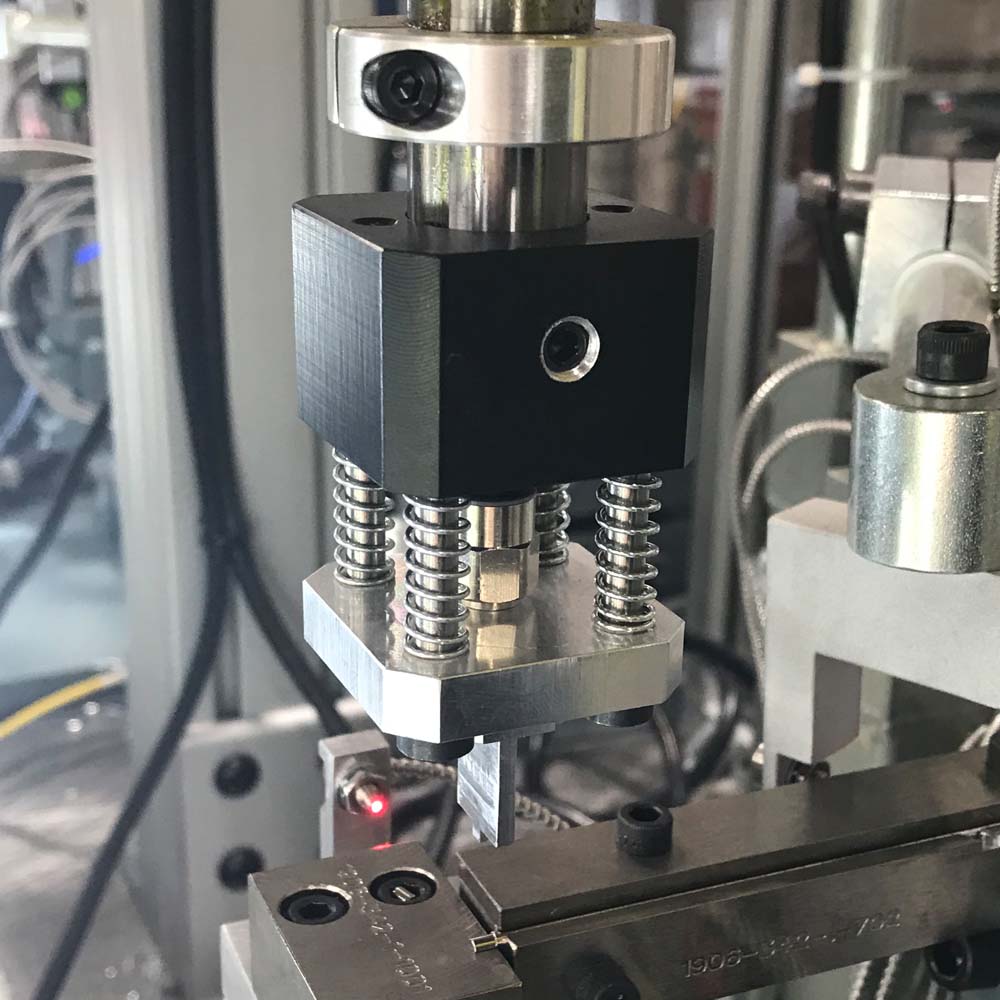
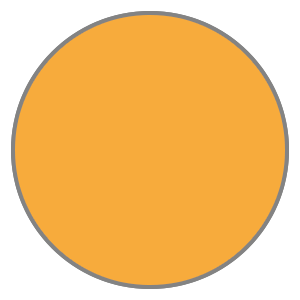
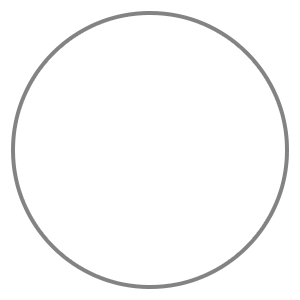
- One gear feeding system.
- The gears are loaded into a bulk supply hopper.
- The hopper delivers gears (on demand) onto a carpet-style parts feeder where they are marshalled into a single lane and singulated at the end.
- Two magnet feeding system.
- The magnets are loaded into a bulk supply hopper.
- The hopper delivers magnets (on demand) into a vibratory feeder bowl which creates a single lane of discharge onto a vibratory linear track where the magnets are accumulated at the end.
- Two gear assembly stations, each comprised of a magnet handling robot, a gear lift & rotate assembly, a vision system, and a Loctite dispense system.
- When a gear arrived at an assembly station the vision system would determine the rotational orientation of the slots.
- Using the vision data, the lift and rotate assembly would rotate the gear to orient the first slot into position.
- The magnet handling robot would pick a magnet from the feeding system and place it into the slot.
- The lift & rotate assembly would rotate the next slot into position. The magnet robot would pick a magnet from the feeding system and place it into the slot. In parallel the Loctite dispense system would apply a shot of glue on top of the first magnet/slot.
- The sequence is repeated for the third slot/magnet.
- Two gear handling robots
- Robot 1 would pick a gear from the end of the gear feeding system and place it at gear assembly station 1, pick the gear from assembly station 1 and place it onto an accumulation fixture (to allow the glue to dry), pick the gear from the accumulation table and place it onto a fixture.
- Robot 2 would pick a gear from the fixture and place it onto gear assembly station 2, pick the gear from assembly station 2 and place it onto a magnetizing fixture, pick the gear from the magnetizing fixture and place it onto an outfeed conveyor.
Result: Premier delivers a custom automated solution that meets the customer’s objectives